Types of ICS
Introduction
Industrial control systems (ICS) are mainstays in the worlds of manufacturing, automation, utilities facilities and more. They make many processes easier, streamline systems and are continually evolving to new heights. An interesting fact about ICS is that it was first born when IT concepts were introduced to currently existing physical controls and it has not let up yet.
This article will detail the different types of ICS, including Programmable Logic Controllers (PLC), Distributed Control Systems (DCS), Supervisory Control and Data Acquisition (SCADA) and Industrial Automation and Control Systems (IACS). We will provide a brief summary of each type of ICS along with a rundown of important information about each type. If this is your first foray into ICS, this article will serve as a great introductory walkthrough.
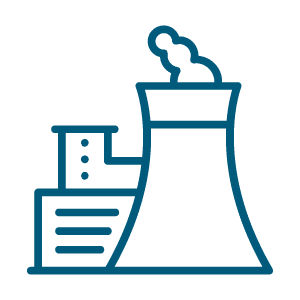
Learn ICS/SCADA Security
What is ICS?
ICS controls much of the world around you. ICS is the computers that control much of critical infrastructure, manufacturing, processing and other automated industries. These systems are essentially the joining of the IT world and the automated world where IT concepts were seeded into the world of physical processing. This has led to a faster, smarter, and safer industrial workplace.
ICS is a general term that describes a diverse group of control systems and instrumentation. That group includes networks, systems and devices that are used to automate or operation industrial processes.
Different types of ICS
There are four main types of ICS:
- PLC
- DCS
- SCADA
- IACS
PLC
PLCs are solid-state ICSes with programmable memory for storage of instructions that monitor inputs and make decisions based on their internal program or logic for automation. An ICS can be PLC-based, where multiple PLCs are networked together in order to share information. Using PLCs in this way also allows for control capability and centralized monitoring.
While some may consider PLCs to be just a component of ICS, PLCs function as the control system itself. Groups of networked PLCs have replaced DCS systems in different industries. PLCs use high-speed discrete control and analog control capability.
DCS
Distributed Control Systems (DCS) are deployed and controlled in a distributed fashion where distributed processes and control systems are controlled individually. The intelligence of these systems is distributed, rather than in one central location as many ICSes have their control positioned. There are controllers between every engineering/operator station and the field instruments that report to it.
DCSes are generally proprietary in nature, meaning replacement hardware, software and other parts need to be ordered from the original vendor.
SCADA
Supervisory Control and Data Acquisition (SCADA) are industrial computer systems that gather and process data and apply appropriate operational controls over long distances. SCADA was developed to handle challenges faced when different information media like phone lines, satellites and microwave transmissions are used.
Typical applications of SCADA systems include critical infrastructure, power distribution and transmission, and pipeline systems. SCADA systems tend toward sharing rather than dedicated use.
Implementing a SCADA system comes with some benefits, including:
- Efficiently processing information at local and remote locations
- Gathering, processing and monitoring data in real-time
- Features human-machine interface that allows for direct interaction with sensors, valves, pumps and other components
- Records information in a useable log file
A strong benefit of SCADA is the ability to report information in real-time to where it needs to go for quick resolution. An example of this is where SCADA reports a high instance of errors to an operator; the operator can quickly pause the machine, review the information and then make the appropriate resolution actions to prevent a loss of product or process.
IACS
An Industrial Automation and Control System is a more basic system that involves safe infrastructure to facilitate information communication and transfers and smart device communication to collect information. IACS uses a combination of sensors, hardware, software and a diversified set of communication methods to render sensor information into usable information.
The big selling point of this type of ICS is the ability of automation to improve the production or industrial process. Some of the examples of how this automation can improve the production process is that it can lead to faster production time, smarter and faster information collection, and an increase in scalability and flexibility. All of these benefits lead to a more optimized production or industrial floor.
Conclusion
ICS is one of the proverbial party favors that long-time advancements in IT and information security have gifted the industrial world with. ICS makes industrial processes more efficient, safe and ultimately more profitable for the business. While there are different types of ICSs and with different features and functionality, all ICSes improve the industrial process to the point where the game has been changed forever.
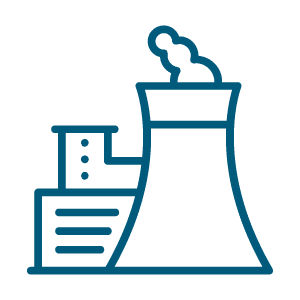
Learn ICS/SCADA Security
Sources
- Types of Industrial Control Systems, Thomas
- Types of Industrial Control Systems, Inst Tools
- Guide to Industrial Control Systems (ICS) Security, NIST
- What is SCADA?, Inductive Automation